Viral Vector Facility
Costa Mesa, California, USA

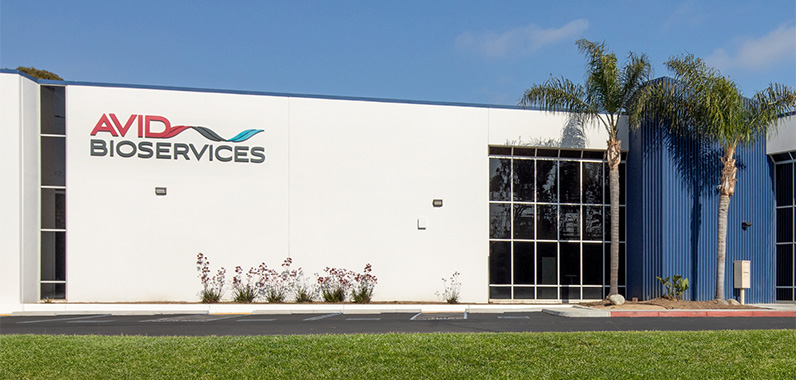
Our purpose-built viral vector facility in was designed from the ground up with the customer and product in mind for better working environments and better results.
Innovating Gene Therapy Development & Manufacturing
Our state-of-the-art viral vector CDMO facility offers comprehensive development and manufacturing services. With a focus on quality and compliance, we support clients from early clinical phases to full commercial production, ensuring successful outcomes for gene therapy products.
- 53,000 ft2 viral vector development and CGMP manufacturing facility
- World-class process development laboratory supporting upstream, downstream, and analytical development
- Two upstream CGMP manufacturing production trains
- Including 6,000 ft2 on-site quality control laboratories
Manufacturing Overview
Upstream
Featuring 50L and 500L SUBs with the ability to scale to 3,000L for suspension culture and batch sizes of up to 40CS10s or 20HS36s with the ability to scale to large fixed bed bioreactors for adherent culture. Dedicated suite for MCB and WCB production.
Downstream
Utilizing advanced platform ÄKTA chromatography skids and TFF systems for efficient and scalable purification.
Fill Finish
Utilizing SKAN isolator technology, programs from early stage clinical to commercial production can be supported with a capacity of up to 2,500 CZ or glass vials per session, accommodating a range of vial sizes from 2R to 50R.
Our Virtual Person-in-Plant Technology
Avid's cutting-edge person-in-plant technology redefines collaboration in viral vector CGMP manufacturing. Our 360° cameras offer a fully immersive, real-time view of operations and reduces gowning requirements. With controllable, wireless communication, and advanced telescoping zoom capabilities, you can remotely monitor every detail of your project. This innovative and customer centric solution streamlines oversight, enhances decision-making, and brings you closer to your manufacturing process — without ever setting foot inside the suite.
- Dedicated HVAC supply per suite
- Grade C classification for processing suites
- Grade B classification for cell banking suite
- SteraMist ionized hydrogen peroxide system
- Integrated iHP system in the viral + suites
- Supports multi-product manufacturing
- Fully automated – short cycle time – 6 log kill
- Utilizes lower concentrations of hydrogen peroxide than traditional VHP, making it safer for employees and equipment
- Spatial segregation for viral +/- suites
- Unidirectional flow for viral + suites
Purpose-built to reduce process risk
- Dedicated HVAC supply per suite
- Grade C classification for processing suites
- Grade B classification for cell banking suite
iHP In-Suite Decontamination
- SteraMist ionized hydrogen peroxide system
- Integrated iHP system in the viral + suites
- Supports multi-product manufacturing
- Fully automated – short cycle time – 6 log kill
- Utilizes lower concentrations of hydrogen peroxide than traditional VHP, making it safer for employees and equipment
Additional Process Controls
- Spatial segregation for viral +/- suites
- Unidirectional flow for viral + suites
Manufacturing Overview
Production Train A
- Suspension culture
- 500L single-use bioreactor
- Adherent culture
- Large-scale fixed-bed bioreactors
Production Train B
- Master and working cell banking
- Suspension culture
- 50L and 500L platform single-use bioreactors
- Adherent culture
- Capable of up to 40CS10s or 20 HS36s batch sizes
Platform ÄKTA Chromatography Skids & TFF Systems
Fill Finish
- Supporting clinical and commercial programs
- Capacity up to 2,500L vials per session
- Capable of filling a variety of vials ranging from 2R to 50R
Purpose-built to reduce process risk.
- Dedicated HVAC supply per suite
- Grade C classification for processing suites
- Grade B classification for cell banking suite
- iHP in-suite decontamination
- SteraMist ionized hydrogen peroxide system
- Integrated iHP system in the viral + suites
- Supports multi-product manufacturing
- Fully automated – short cycle time – 6 log kill
- Utilizes lower concentrations of hydrogen peroxide than traditional VHP, making it safer for employees and equipment
- Additional process controls
- Spatial segregation for viral +/- suites
- Unidirectional flow for viral + suites
Process & Analytical Development Lab
Our viral vector CDMO process development lab is equipped with advanced upstream and downstream capabilities to support diverse project needs. This state-of-the-art facility ensures precision and scalability in viral vector development.
Upstream capabilities include:
- Benchtop bioreactors
- 50L and 500L single-use bioreactors
- Multi-layer vessels for efficient production
Downstream capabilities include:
- Multiple ÄKTA-based chromatography skids
- Tangential flow filtration (TFF) systems
- Ultracentrifuges available to specific project requirements
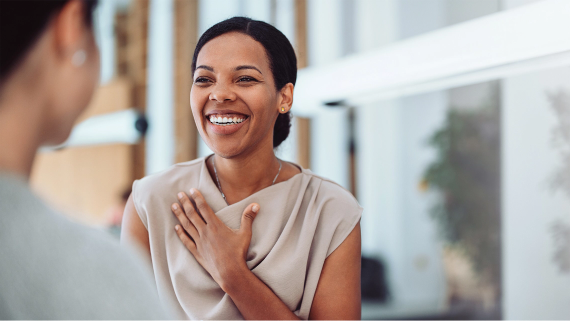
Why Avid?
Your life’s work is in good hands.
Our experts are fully committed to your success, advocating for you and helping to minimize risk.